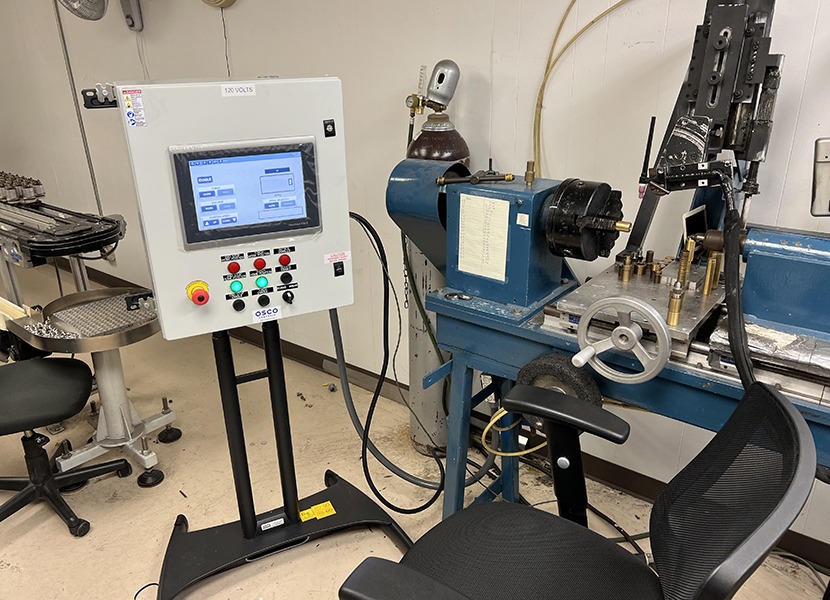
Revolutionizing Welding Processes: Implementing a Flexible Controls System for Standardization
Challenge
OSCO Controls partnered with a safety component manufacturer on a retrofit for their automated welding lathe. The company wanted to modernize their processes to standardize their numerous welding requirements for different parts and needed a controls system that could provide the flexibility and the program logic to call up 1,000 plus part recipes.
Solution
OSCO Controls engineered a control panel adaptable to a variety of welding recipes for the parts applications. Their new controls featured a larger touchscreen HMI, emergency stop and pushbutton devices, 1000+ part recipes and overall ergonomic improvement.
The newly designed control panel improves the welding performance and simplifies the various welding applications. The customer can call up 1,000+ different parts that they manufacturer by serial number and enter it into the touchscreen to call up the pre-programmed routine (recipe) for welding arm deployment and turning lathe rotational speed settings. The new panel also allows the customer to enter in their own custom recipes.
Result
OSCO Controls helped the customer upgrade their control system to improve efficiency and faster parts production on their welding lathe.
Let us upgrade your legacy manufacturing equipment and experience the difference!
Case Study Photos
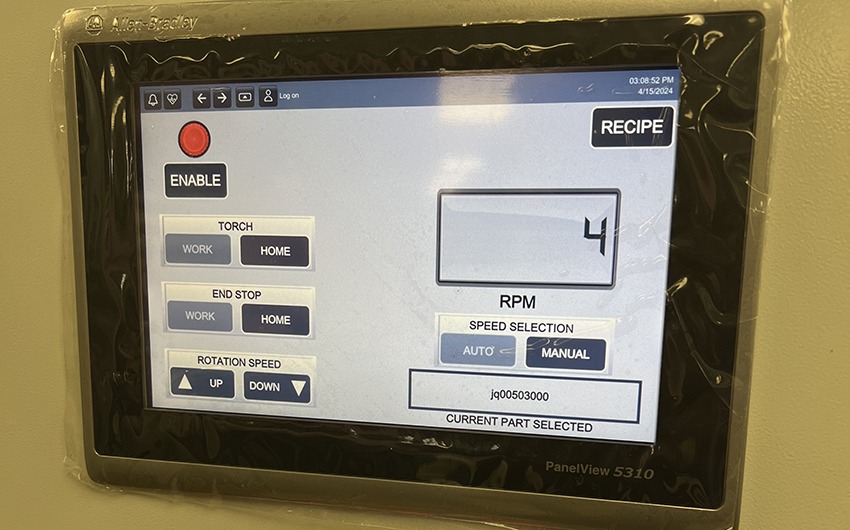
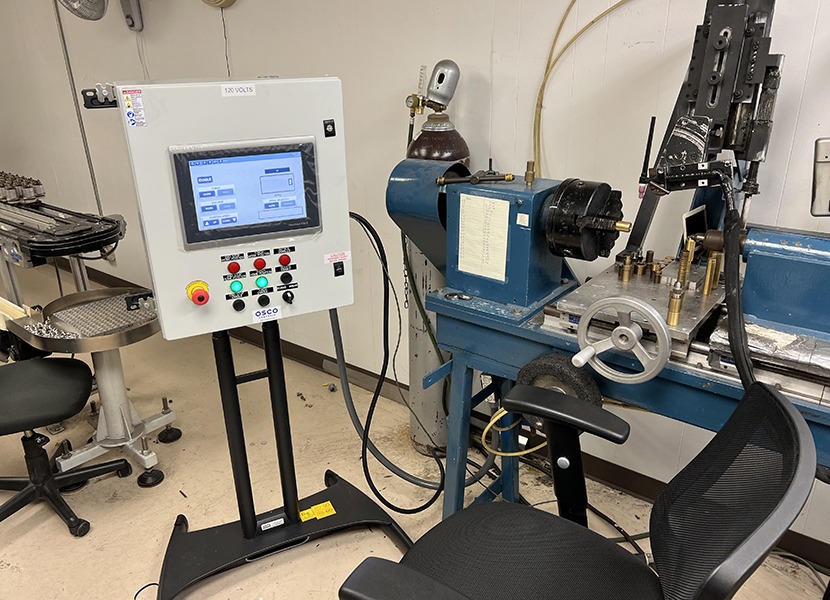