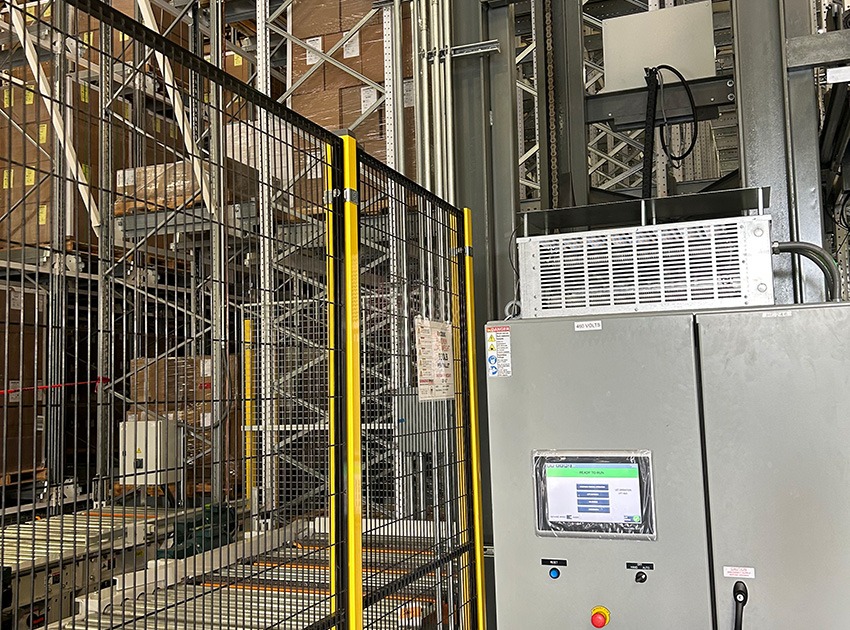
Custom Controls Integration for Automated AGV Rack Retrieval and Storage System
Challenge
The end user of this project is a cutting-edge company delivering fully automated liquid handling systems to leading manufacturers. They specialize in the development and manufacturing of precision measurement devices, automated liquid handling workstations, and sample management systems. Having firsthand experience with supplying automated solutions, the company found themselves needing to improve their manufacturing workflow with a new approach for integrating and automating multiple systems to work together.
The company relies on AGVs to move pallets around their facility. They wanted an automated solution for moving AGVs and pallets to their multi-story rack system to speed up the process for retrieving and storing palletized materials. They will be using a Vertical Reciprocating Conveyor Lift (VRC) to take AGVs and Pallets to their designated location within the rack system. OSCO served as a mediator for all systems outside the inventory management, and it was our job to integrate these systems to operate autonomously through network commands.
Solution
Our task was to communicate with the vendor that handled the inbound and outbound conveyors. This involved close collaboration with them to determine when there was a pallet to pick up and communicating with them when we were commanded to discharge a pallet on the outbound side. To inbound, we would communicate with the inventory management system that a pallet was available and ready for pickup. Upon being commanded to go to the position, we would capture and package barcode information for the specific product that was being conveyed into the VRC lift, send a signal to start conveying to the inbound conveyor controller, and create custom tracking data so that the inventory management system could track the pallet through the rack system. Once the pallet was onboard the VRC, the inventory management system would command us to go to the level where that pallet was to be stored. Once we completed the move to the commanded level, we would then send a message through the network stating that the command to move to a level had been completed which the WMS (warehouse/inventory management system) would acknowledge and immediately follow up with a command to discharge the pallet to the conveyor associated with the level the VRC was at. This was done in reverse on the outbound side.
The project collaboration was unique as it involved communicating directly to the vendors controller anytime AGVs were being commanded to interface with the lift or level conveyors. At all times, the VRC controls were communicating to the AGV controller the status of each drop zone (level conveyors and 15 staging lane areas inside the storage racks). These status notifications served as permission for the AGV to either drop or pick a pallet from a specific location. When the AGV requested to drop a pallet in a specific location, the VRC would turn that into data to be sent to the WMS to essentially know that there is now a pallet at that location and here is the tracking info for it. When the WMS determines what to do it would then command the VRC to convey onto the VRC platform, move the pallet to a specific level, discharge to a conveyor or out of the system. The AGV interface also served as permission for the AGVs to dock and undock from the VRC. This served to transport AGV from level to level for various reasons (maintenance, charging, the need for an extra AGV on a specific level due to high volume, etc.).
Project highlights:
• Implemented a dual feedback positioning system. The mechanical design sought to significantly reduce the negative impact of chain stretch; the dual feedback system ensures that any stretch is eliminated. The carriage essentially floats when conveying pallets and automatically stays at the precisely commanded position even when transferring heavy loads. This also allows AGVs to easily move on and off the VRC (they have a very low profile and have a very small tolerance for how out of level 2 mating surfaces can be…i.e., the level conveyor and carriage conveyor).
• The WMS integrator used their standard code base which used a very specific structure written in C#. To receive commands from them and turn them into meaningful actions performed by the VRC we had to parse large arrays with custom codes that correlated to specific actions. Once these actions were completed, we had to populate arrays and send them back through the network to the windows machine that they were using to control everything. These arrays served as confirmation that we had successfully completed the action that was requested. They would then send another array that would serve as an acknowledgement for our message which would serve as a condition to get the VRC into a state where it could receive another command to perform an action.
• The AGV supplier had a very rigid system that we had to figure out a way to make our system communicate with theirs. Our controls engineer on the project basically built a system that communicated directly with their controller on one side of the network and a gateway to their system on the other. Connected to the other side of the gateway was our Allen Bradley control system architecture. In doing this, our controls engineer could write to allocated registers using Ethernet/IP and parse those registers in their system which could then be passed on to the AGV controller and turned into meaningful data. The process was reversed for AGV to lift communications.
• This system operates autonomously 98% of the time. Very little operator intervention will ever be needed.
• Our system communicates with all other control systems on the project. 80% of all system communication goes through our system in one way or another.
Result
OSCO specializes in making complex systems work together. Our team used their deep knowledge and expertise to provide a solution to integrate different systems into a cohesive operation. We were able to work effectively with other integrators on the project resulting with the customer being very satisfied with the knowledge OSCO brought to the table.
Case Study Photos
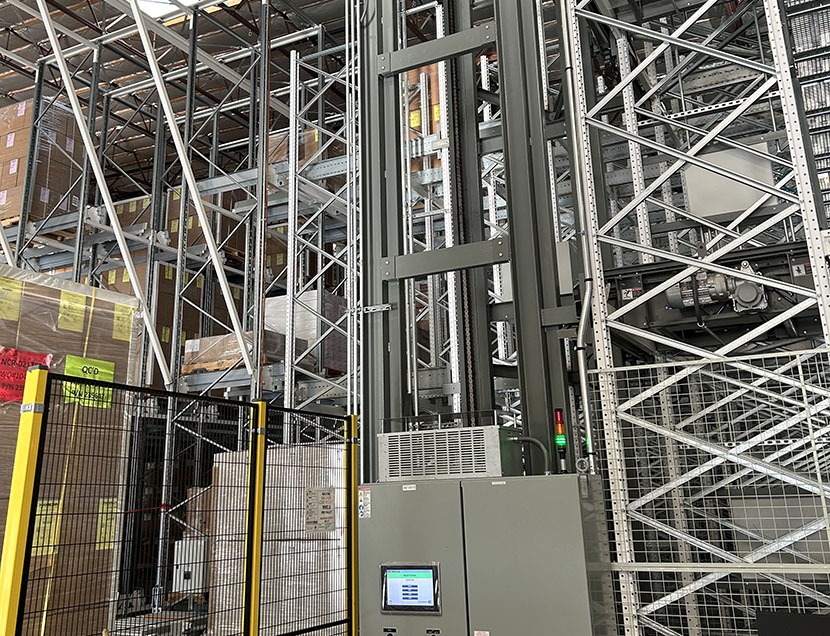
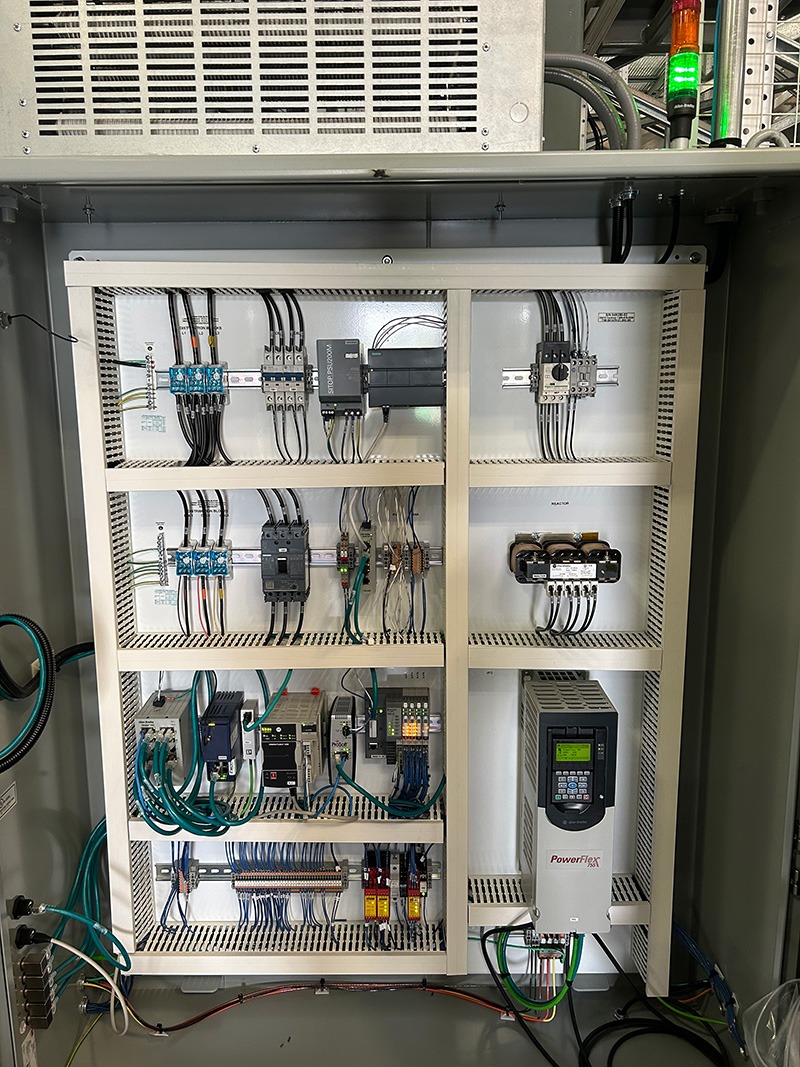
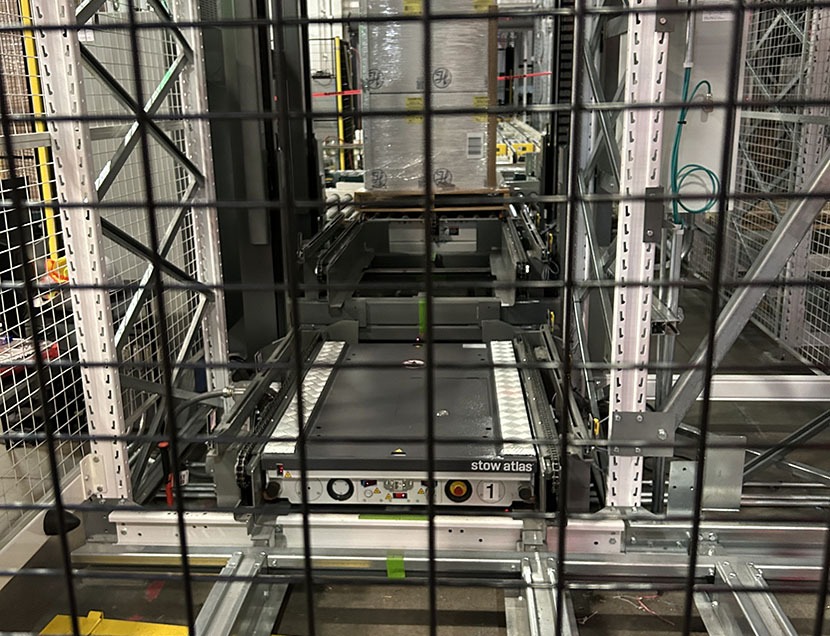
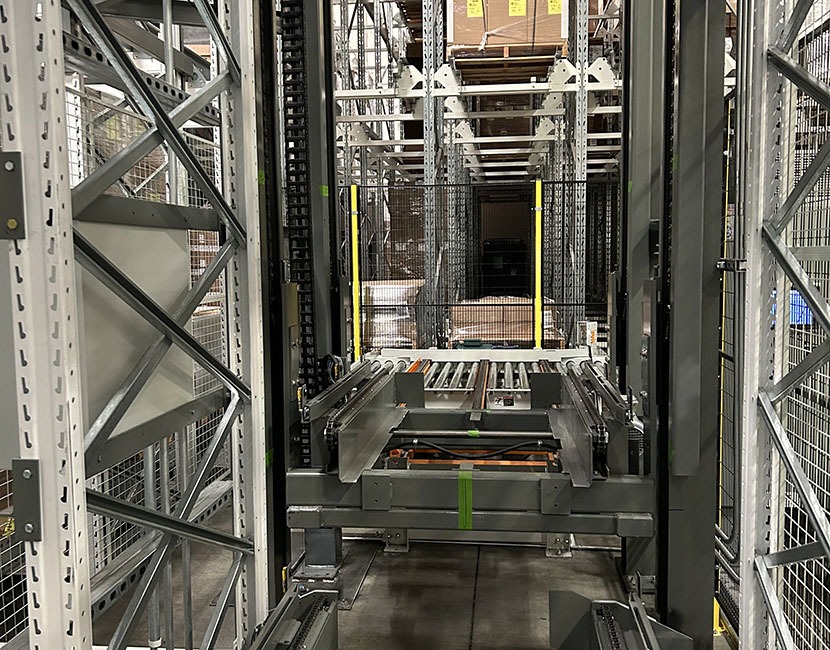
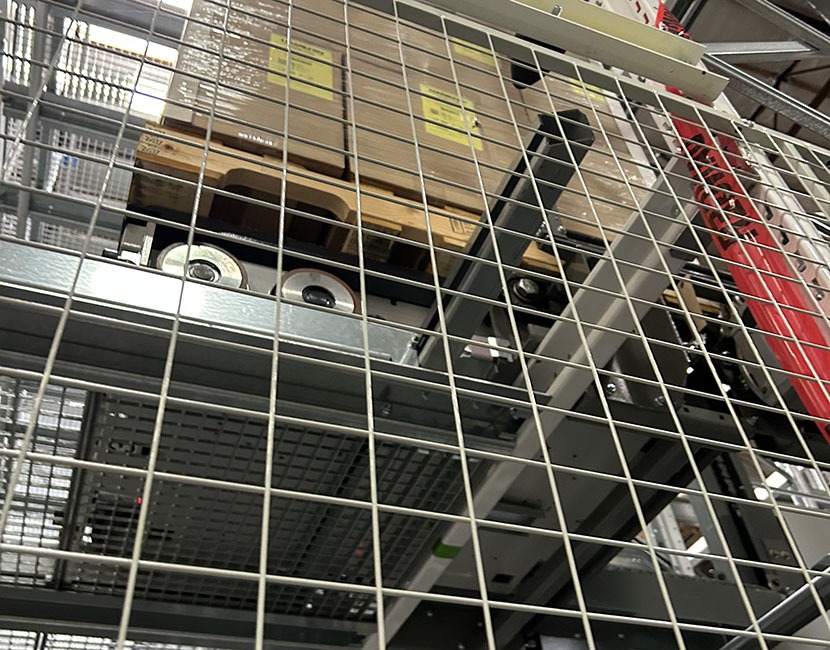
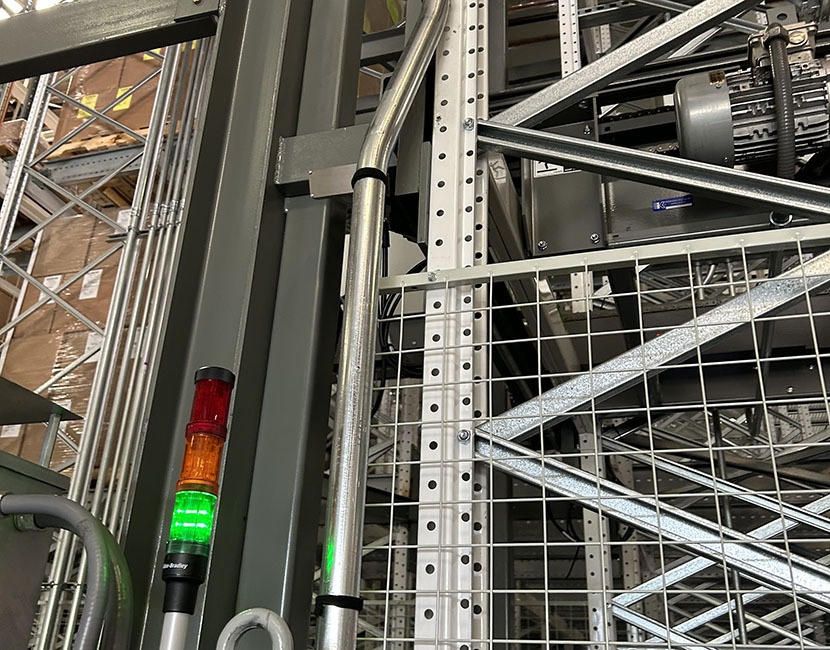
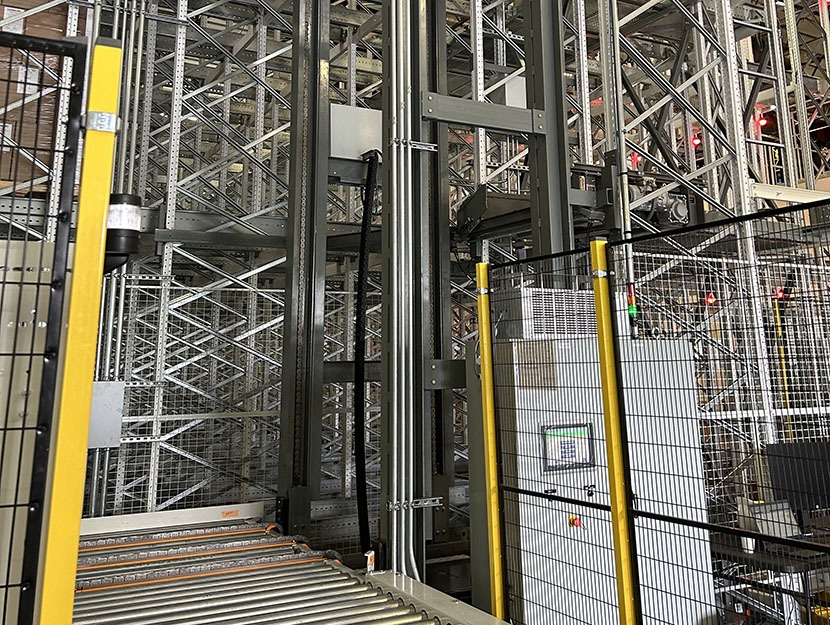
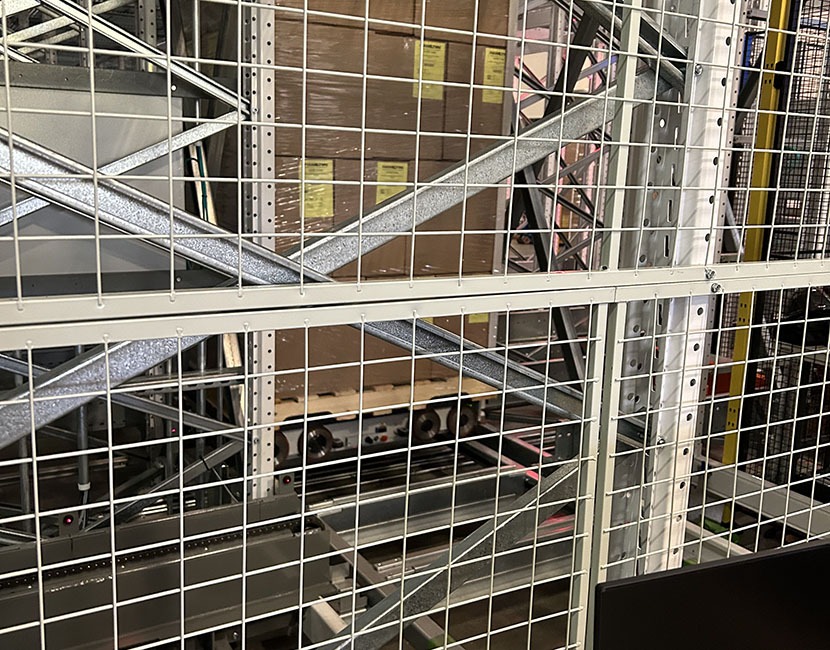
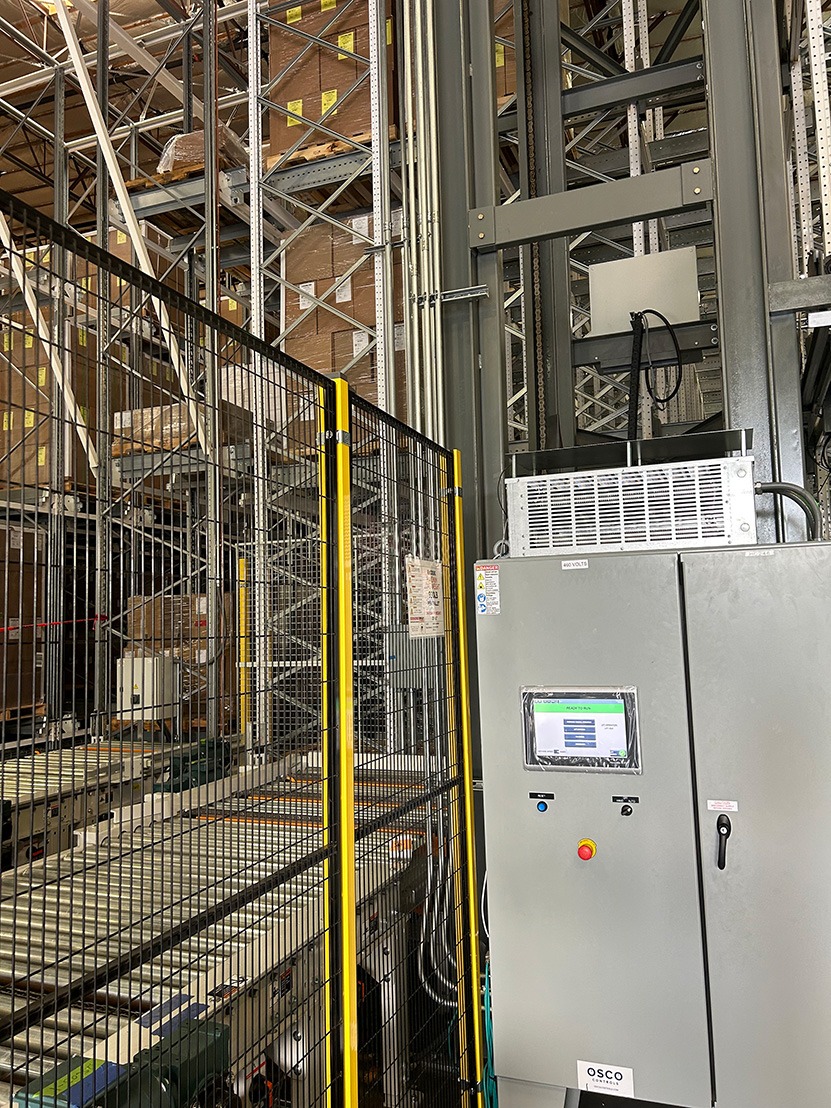